Инновации из мусора не спасут от шума и вибраций
30 янв. 2024
Появление на рынке виброизолирующих материалов изделий из резиновой крошки и полиуретанового клея вызвало вопросы у потребителей. Так ли все хорошо, как пишут компании с названиями “Эко-…” и “Ультра-” и т.д.? По заявлениям производителей это материал, "который по своим свойствам не уступающий лучшим образцам иностранных и отечественных производителей антивибрационных материалов". 
А может ли быть правдой то что написано в творениях маркетологов компаний с названиями “Эко-…” и “Ультра-” и некоторых их последователей? Неужели в самом деле материалы под привлекательными названиями “Вибро-” и “...рез” обладают являются аналогами, в т.ч. зарубежных, виброизоляционных материалов Sylomer, Vibrafoam, Gener, Nowelle и могут обеспечить тот же высокий уровень характеристик?
Из информации на сайтах производителей становится понятно, что виброрезы - это композиция, изготовленная из резиновой крошки, произведенной из автомобильных шин и олигомеров на основе изоцианатных материалов.
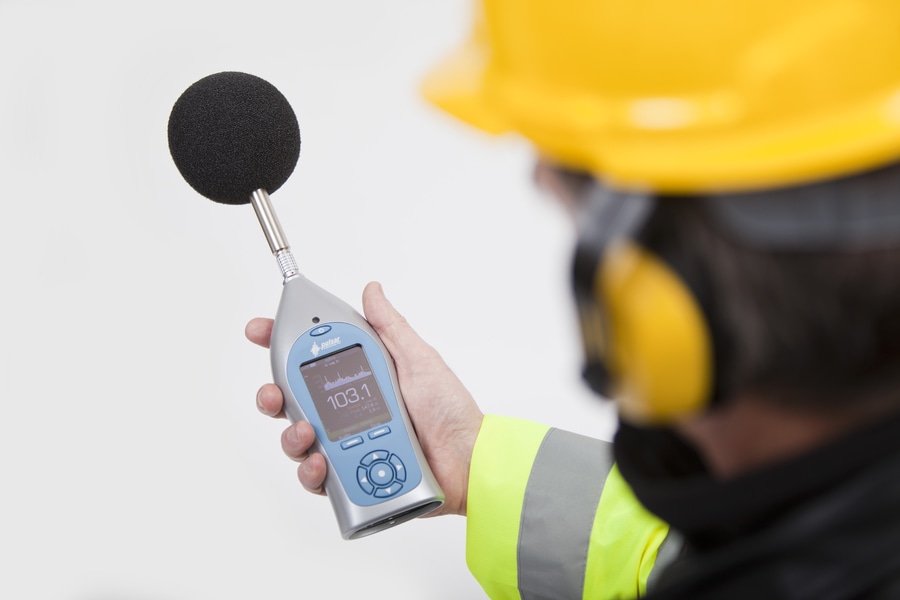
Настораживает, что производители представляют свои антивибрационные материалы как инновационные высокотехнологичные продукты с уникальным комплексом свойств, не акцентируя внимание потенциального клиента на том, что большая часть составляющих этих материалов представляют собой дробленые шины со свалки. Попробуем разобраться в этих вопросах.
Из чего изготовлен виброрез
В производстве “антивибрационных” материалов виброрез используют резиновую шинную крошку, т.е. материал произведенный методом дробления автомобильных шин, поскольку такая крошка самая дешёвая. Рецепты резин, используемых при изготовлении автомобильных покрышек базируются на комбинациях каучуков - натурального и синтетических изопренового, стирольного и дивинильного. Шинные каучуки, благодаря своей химической формуле, имеют высокие среди показатели эластичности, т.е. низкое внутреннее трение в молекулах полимера, т.н. гистерезис. Это важно для автошин, которые должны амортизировать удары, защищая тем самым подвеску автомобиля. Но для демпфирования вибраций они бесполезны.

Для вибродемпфирующего материала, в частности демпфирующей пластины ПД-С-Ф-10-500х500, которая изготавливается по ТУ 22.19.20-133-75233153-2022, необходим высокий гистерезис, за счет чего, ввиду высокого внутреннего трения внутри полимера, имеет место высокий уровень потерь механической энергии, что приводит к поглощению (рассеиванию) энергии колебаний. Такие характеристики можно получить применением эластомеров на основе синтетических нитрильных каучуков и полиизобутиленовых полимеров, у которых гистерезис высокий - следствие химической структуры макромолекул основной полимерной цепи.
Как обстоят дела с качеством резиновой крошки
Химический состав резиновой крошки, из которой делают виброрез, зависит от сырья, из которого она изготовлена, т.е. от типа автомобильных шин (легковые, грузовые, крупногабаритные, а также летние, зимние и всесезонные и т.д.) и даже от той части той самой шины (протектор, боковина, борт и т.д.), который в процессе дробления превратился в крошку. А поскольку состав резин упомянутых элементов покрышки различаются, то и физико-механические показатели резиновой крошки различны. Но потребитель “антивибрационного” виброреза об этом редко догадывается, а им никто и не объясняет.
В отличии от виброреза и их аналогичных продуктов, у демпфирующих эластомерных пластин, таких как ПД-С-Ф, которые изначально разрабатывались в качестве виброзащитных и виброгасящих материалов, состав всегда идентичен, поскольку в составе во-первых отсутствуют продукты вторичной переработки, а во-вторых применяются только первичные каучуки бутадиен-нитрильного ряда, а также ряд полимерных пластификаторов, в т.ч. фактис. Поэтому эксплуатационные характеристики, в том числе способность к поглощению энергии вибрационных колебаний, у виброзащитных материалов от “Вулканикум” стабильны.
Что негативно влияет на работоспособность виброреза
Применение при производстве виброрезов материалов, находящихся в разном агрегатном состоянии, резиновой крошки и изоцианатного олигомерного связующего, делает материал многофазным, т.е. сложно вести речь о его монолитности. Даже приняв во внимание, что крошка сможет в процессе изготовления “присоединится” к связующему олигомеру, благодаря неравномерности распределения активных центров по поверхности крошки, а также различного параметра растворимости, ухудшающего совмещение различных материалов, в т.ч. из-за использования в одной системе полимеров разных типов, трудно добиться, чтобы каждая частица крошки полностью “покрылась” связующим составом. Из-за этого в массиве виброреза неизбежно присутствуют микропоры. Справедливость этого утверждения подтверждают показатели плотности виброрезов - 730 кг/куб.м, что в 1,5 - 2 раза ниже, чем у классической резины (показатель плотности приведен для антивибрационного материала Виброрез-Н). А так как резиновая крошка распределена во всем объеме связующего материала, в том числе и на поверхности, становится понятным, что виброрезы представляют собой систему с открытыми порами.
Учтем, что виброиоляцию помещают под фундаментами, т.е. либо в землю, либо в нишевые пространства, где нет циркуляции воздуха, и лежат, как правило, ниже уровня пола. В этих условиях трудно избежать воздействия на виброизоляционный материал воды. При этом будет иметь место не набухание самой резины в воде (к чему основные виды шинных резин устойчивы), а «механическое» проникновение воды в имеющиеся в материале микропоры.
В зависимости от размеров частиц резиновой крошки, распределения частиц разного величины в массиве материала и количества воды, попавшей внутрь массива, эксплуатационные характеристики виброизоляционного материала будут меняться. При этом, поскольку вода практически несжимаемый материал, и ее наличие внутри прежде всего радикально меняет именно динамические характеристики изделия. При отрицательных температурах вода, находящаяся в порах замерзает и, за счет увеличения своего объема, может приводить к мало предсказуемым локальным повреждениям структуры материала, с дальнейшей угрозой разрушения.
Обратимся к связующему, которое представляет собой изоцианатный олигомер, который структурируется в процессе отверждения изделия. Пониженная гидролитическая устойчивость полизоцианатов - известный факт, осложняемый еще и тем, что гидролиз полимерных цепей еще сильнее в случае наличия в воде растворенных солей, т.е. практически всегда, поскольку редко антивибрационные материалы работают в среде дистиллированой воды. Так как гидролитического действия водных растворов солей на изоцианатный полимер трудно избежать в условиях эксплуатации, этот комплекс негативных факторов приведет к уменьшению эффективности виброзащиты, а затем и к разрушению всей системы виброизоляции и сокращению срока службы материала с полиизоцианатным связующим.
Обман потребителя - это допустимо?
Вывод "инновационного" материала из сырья со свалки маркетологи начали с информационной атаки на лидеров рынка виброзащитных стройматериалов. Отчаянные маркетологи, нанятые для продвижения виброрез, объявили материал из резиновых отходов “аналогом” импортных виброизоляционных материалов, в частности Sylomer, Vibrafon и даже Nowelle. Любой грамотный специалист и даже квалифицированный потребитель объяснит, что материал из резиновой крошки и уретанового связующего имеет мало общего как с пенополиуретанами от Getzner и Kraiburg, так и с нитрильными резинами Nowelle.

Т.е. налицо либо продуманный обман потребителя и нечестная конкуренция, либо низкий уровень грамотности составителей рекламных текстов и их заказчиков, непонимающих смысл слова "аналог".
Если же вспомнить все, что было написано выше, то речь можно вести лишь о том, что Виброрез - это аналог напольных покрытий типа Masterfiber - производителя напольных покрытий и покрытий детских площадок именно из резиновой крошки.

Справедливости ради, отметим, что Мастерфайбр, заботясь о качестве и стабильности своих продуктов, давно ушёл от использования шинной крошки со свалок, а использует специально приготовленный материал из каучуков EPDM, оставив мусор своим малоудачливым конкурентам и различным "инноваторам".
Сравним виброрез с демпфирующими материалами
Заявляемые “антивибрационные" виброрезы проигрывают специально разработанным демпфирующим эластомерам как на основе бутадиен-нитрильных каучуков, так и пенополиуретанам, поскольку материалы из крошки обладают низкими показателями как несущей способности, так и способности к поглощению вибрационных колебаний. Так, для получения требуемого уровня поглощения вибраций вместо блоков виброрезов толщиной в 50-60 мм достаточно использовать 20 мм демпфирующей эластомерной пластины
Традиционные эластомеры, изготовленные по технологии высокотемпературной вулканизации под избыточным давлением, и которые обычно используют для демпфирования вибраций, в т.ч. ПД-С-Ф-10, монолитны, практически не впитывают воду и устойчивы к гидролизу. Т.е. можно говорить о надёжности современных вибродемпфирующих эластомерных пластин.

Можно сделать вывод, что применение в “антивибрационном экоматериале” шинной крошки, ведёт к высокой нестабильности эксплуатационных характеристик изделий, к минимизации способности материала к вибропоглощению. Применение в качестве базового материала эластомера с высокой эластичностью - крошки из резины на основе каучуков изопренового, дивинильного и бутадиен-стирольных, не позволяет изготавливать виброзащитный материал с высокими показателями поглощения энергии колебаний, т.е. материалы класса виброрезов вряд ли стоит именовать вибродемпфирующими.
Удивительный срок службы виброреза
Взглянем на прогнозируемые сроки эксплуатации виброрезов. Удивительно, но они не превышают, исходя из данным приводимых на сайте производителя виброзеза и в сопроводительных документах, 5 лет. При этом разработчики рекомендуют использовать их в фундаментах зданий, что видится весьма смелой рекомендацией, если учитывать срок эксплуатации некоторых сооружений в не один десяток лет. Что делать, к примеру, со зданием по истечение тех самых 5 лет, как проводить замену материала, срок гарантии которого вышел - вопросы на который ответов нет.
Для сравнения приведем аналогичные показатели для классических демпфирующих эластомерных пластин, которые составляют по экспериментально-прогностическим исследованиям от 30 до 50 лет и более.
Выбор для потребителя непрост
Потребитель оказался перед сложным выбором: либо взять нестабильный материал с трудно предсказуемыми характеристиками типа виброрез, изготовленный на 90% из отходов и материалов со свалки, поверив в сказку от маркетологов - сомнительное, но бюджетное решение, либо сделать разумный выбор в пользу качественного, надёжного классического вибродемпфирующего материала, к примеру демпфирующая эластомерная пластина ПД-С-Ф-10-500х500, производство которой ведется в соответствии с ТУ 22.19.20-133-75233153-2022, и гарантированно обеспечить вибрационную защиту объектов на все время эксплуатации защищаемого здания или оборудования.
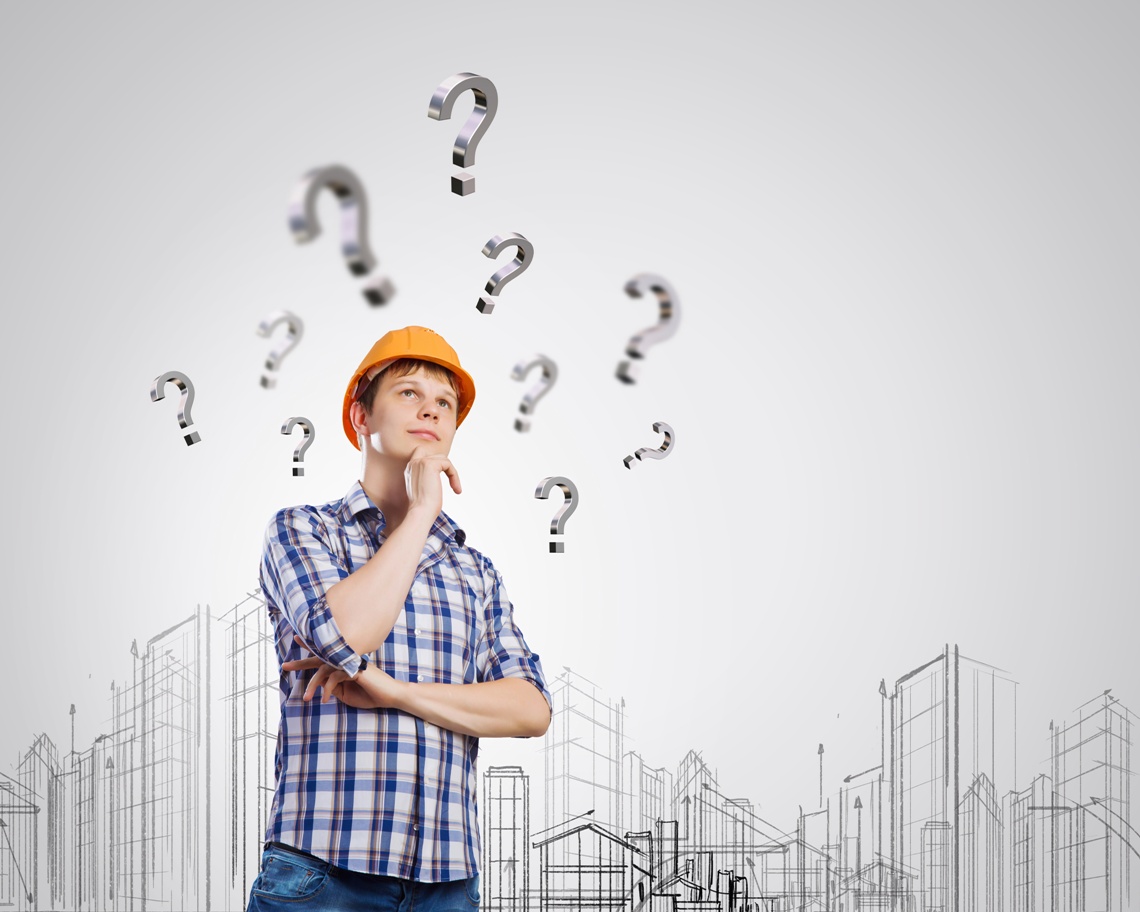
вернуться в список»